New depressant for Cu-Mo separation with better results and less chemical reagents cost
INTRODUCTION
Copper-Molybdenum ore flotation process is usually divided into two stages: Cu-Mo bulk flotation and Cu-Mo separation flotation . Recovering the target minerals as much as possible, which means to improve the recovery of copper and molybdenum is the most significant thing in Cu-Mo bulk flotation process.
Traditional Cu-Mo depressants used in Cu-Mo separation are hazardous inorganic chemicals. Mining operations in Dexing, Chinese biggest copper mining plant, consumes a large quantity of sodium hydrosulphide (NaSH) in its Cu-Mo circuit. While the bad smell and higher dosage of reagents leads to notorious working conditions and environmental pollutions.
Continuous efforts have been made to find a good alternative for the notorious hydrosulphide to meet the demand of the client. The main target is to maintain the same or better metallurgical performance while lowering operation cost and reducing environmental impact .
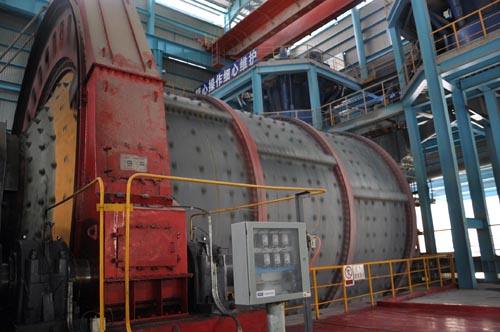
Numerous kinds of reagents have been tested either in laboratory or pilot scale test in the plant, which includes modified and newly synthesized in the lab. Actually hydrosulphide has been applied in this plant more than ten years, while it has some disadvantages as followed:
(1) Bad operating condition due to the notorious smell of reagent;
(2) Higher dosage and sticky foam;
(3) Easy to oxidation leading to fluctuation of metallurgical performance;
(4) Not good for fine particle separation
The process flowsheet and reagent have been modified to minimize the operating cost while maintaining similar or better metallurgical performance with the following features:
(1) Easy to operate with its good solubility and lower dosage;
(2) Selective depressing CuFeS2 at pH 8-9 while no depression on MoS2;
(3) Better metallurgical performance with lower reagents consuming;
RELEVANCE
The innovative technology and reagents developed in this project could be used in other similar Cu-Mo mining plants around the world, as the metallurgical performance could be improved with less operating cost, as well as less environmental impact to the surrounding community.